Digital or Conventional Flexible Packaging: What’s Best for Your Brand?
If your product is packaged in flexible material like a plastic pouch, film or bag, you have tons of options thanks to digital printing as well as techniques like flexography and gravure. But which technique is best for your packaging? We have a lot of experience here, so we can help.
Digital Printing for Flexible Packaging
Why go digital? It’s perhaps the least expensive, fastest option for many reasons. Digital printing uses electro-ink or inkjet technologies, not printing plates. This takes setup charges, waste and long lead times out of the equation. Digital printing is ideal for short to medium runs (not long runs) and printing variable data (think multiple versions). This method also handles almost all colors, gradients, shadows, and other complex design elements well.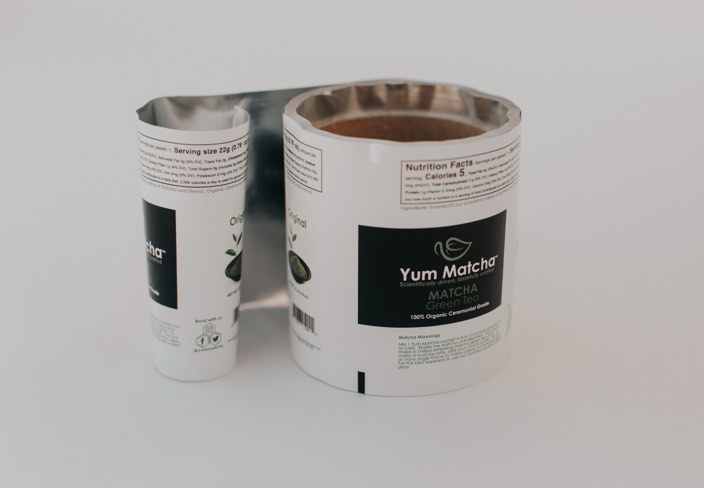
Flexographic (aka Flexo) Printing for Packaging
This method of printing uses flexible plates to print designs on non-porous materials such as plastic. Flexo printing is commonly used for food, cosmetics and consumer goods that use bags, pouches and other forms of flexible packaging. This printing method handles solid colors well but special attention must be used when incorporating gradients and shadows. Flexo printing can be done at a relatively quick speed for a reasonable price. Ideal for medium and large runs with reasonable lead times, flexo printing may be best when you have limited varieties and designs to print. Typography is also your friend! Explore the many ways you can use words to help your brand stand out. A high-quality printer will ensure your words — and any unique design elements — come out clean and sharp so your brand looks high quality.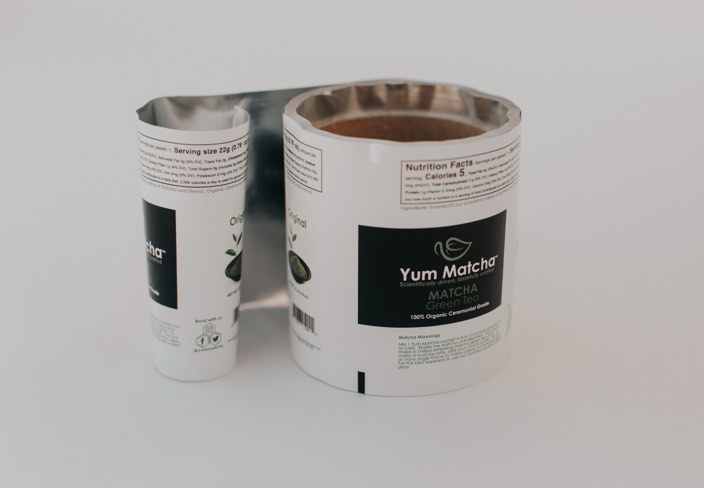
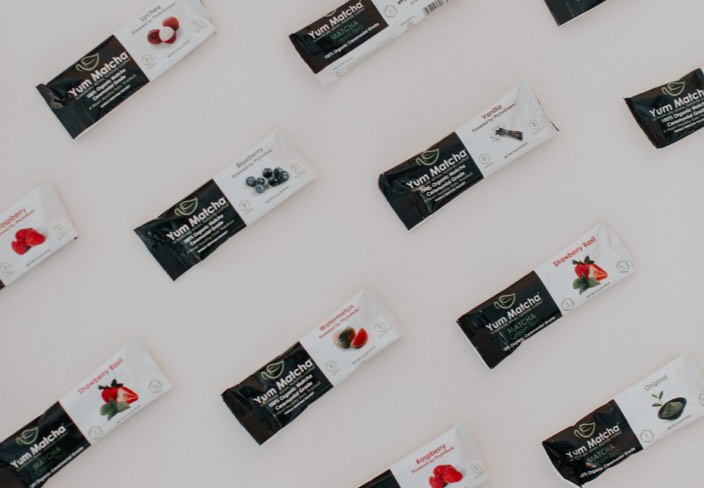
Does Your Flexible Packaging Need to Be Produced in a GMP Facility?
Most likely, yes. GMP (Good Manufacturing Practices) are a standard of manufacturing practices for both human and veterinary drugs, as well as food products. If your packaging will come into direct contact with food (such as a preprinted beef jerky pouch or a label you place on an apple), it needs to be produced in a GMP-compliant facility. Ask your packaging supplier if they can comply. (Hint: a GMP facility will always have a certificate from a third-party auditor saying the facility is in compliance for a certain period of time.)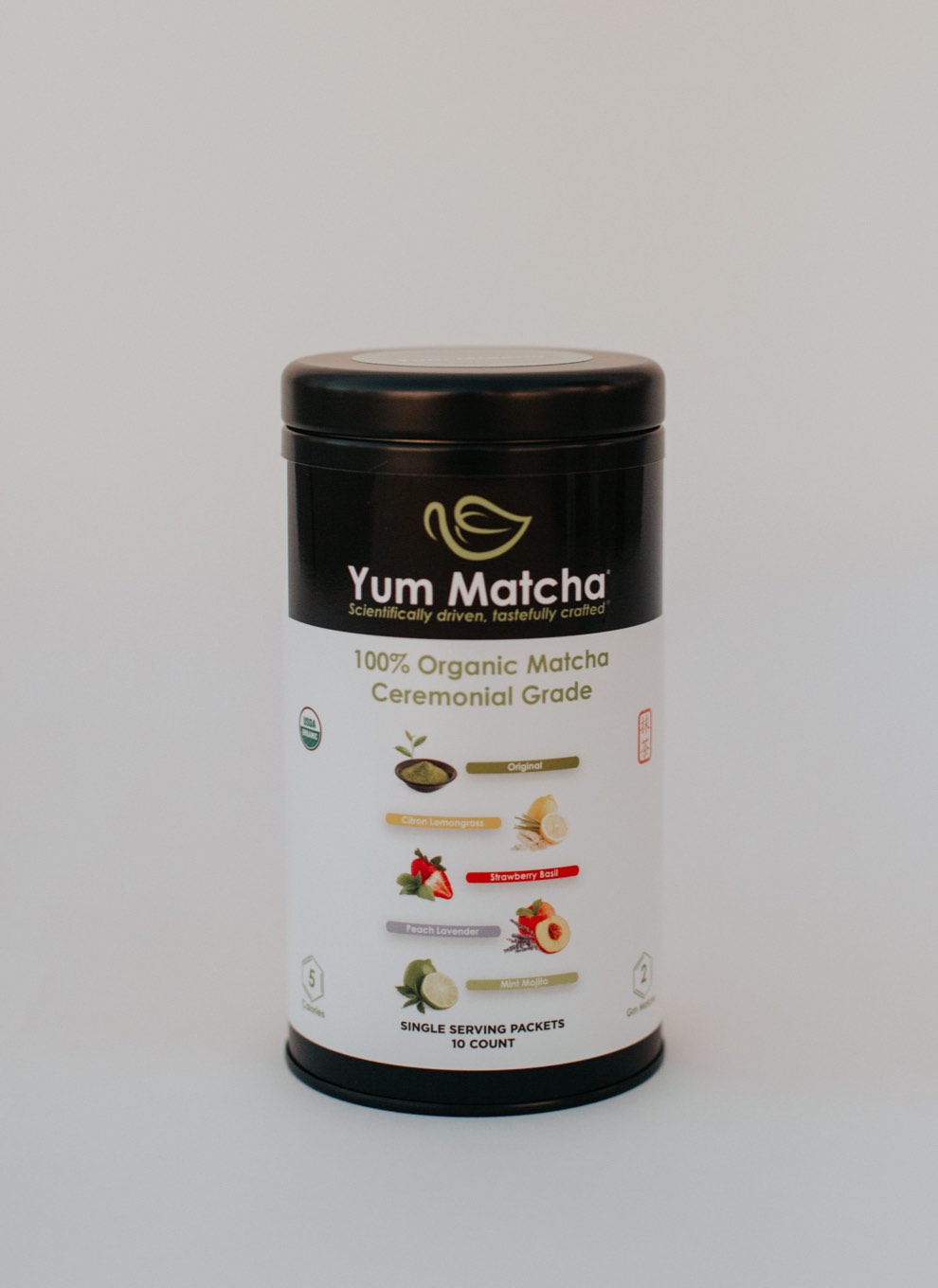
State-of-the-Art Flexible Packaging Solutions
Do you need 1,000 or 100,000 flexible pieces? One version or 20 versions? The Label Shoppe has your back. Our 15,000-square-foot, state-of-the-art facility is fully climate controlled, including all raw material, production, and finished-good storage areas, so your flexible packaging won’t curl, smudge or underperform due to variable temperature and humidity. We offer digital and flexographic printing for flexible packaging as well as a nearly unlimited spectrum of colors, premium finishes, and 100% pharmaceutical-grade defect inspection. Our superstar staff checks every detail, from color matching to bar codes, for perfection and performance.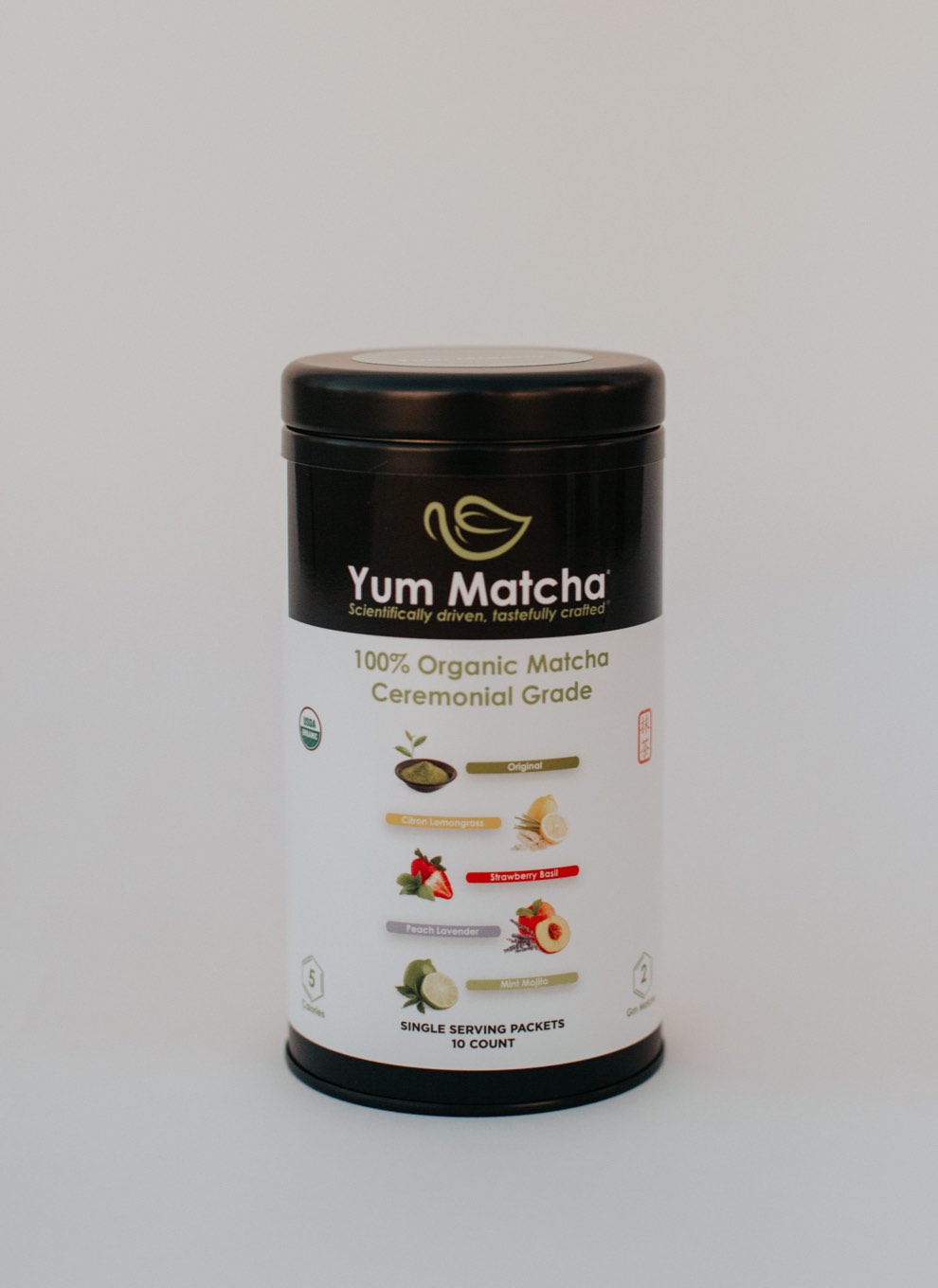
Does Your Flexible Packaging Need to Be Produced in a GMP Facility?
Most likely, yes. GMP (Good Manufacturing Practices) are a standard of manufacturing practices for both human and veterinary drugs, as well as food products. If your packaging will come into direct contact with food (such as a preprinted beef jerky pouch or a label you place on an apple), it needs to be produced in a GMP-compliant facility. Ask your packaging supplier if they can comply. (Hint: a GMP facility will always have a certificate from a third-party auditor saying the facility is in compliance for a certain period of time.)Get In Contact
Request a Quote
Subscribe To Our Newsletter
We noticed you’ve visited our site recently, please consider signing up for our newsletter